June 24th, 2024
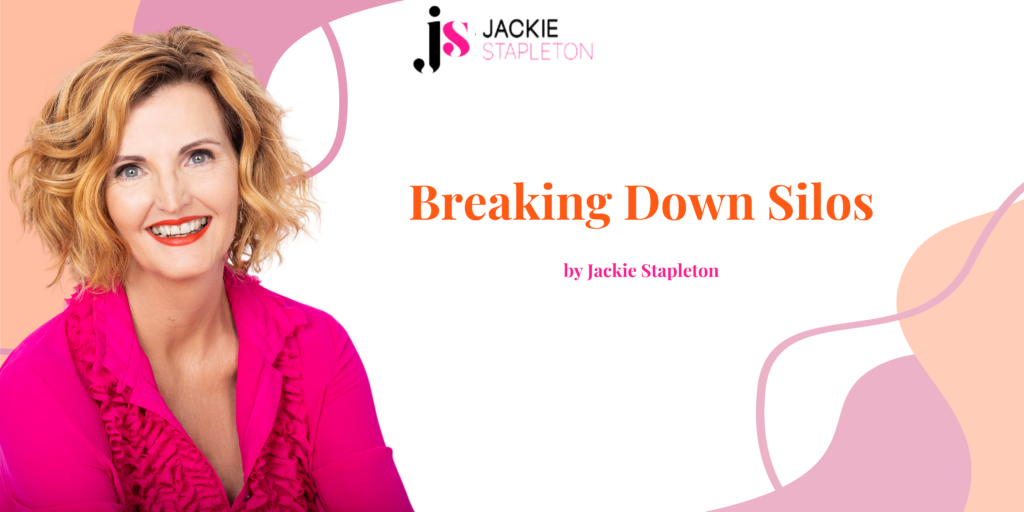
————
From 1998 to 2008 I worked for a software development company. I had a mix of roles, from support, training and finally quality manager. When I came on as the quality manager, I had the benefit of working within the business as an employee in different roles and despite the cutting-edge product that we offered our clients I knew that behind the scenes there was a significant challenge that needed to be overcome; a siloed work culture that hindered collaboration and hindered their progress.
The company operated with distinct departments, each focused on their own objectives and tasks. The software development team worked away in their corner, rarely interacting with the quality team, and the customer support team was disconnected from the rest of the business, coming up with their own systems and processes without collaboration with the rest of the business. This siloed approach was resulting in disconnected communication between different departments and therefore errors and issues occurred which of course ultimately impacted our customers.
Nonconformances Drive Improvements
After I consistently raised nonconformances in my internal audits across the different departments, it was identified through root cause analysis and corrective action implementation that the common ground here was that each department was running their ‘own little business’ and had siloed themselves from everywhere else. After a management review meeting, where I presented these findings the leadership team decided to embark on a transformative journey. Their goal was a company where collaboration thrived, where every team member understood the impact of their work on others, and where shared goals united them towards a common purpose.
Process Approach Breaks Down Barriers
To do this, the business adopted a process-oriented approach. They introduced cross-functional teams, breaking down the barriers that had previously separated departments. These teams were made up of individuals from different backgrounds, collaborating closely on projects from start to finish. As the new process-oriented approach took hold, I started to notice a change. The software development team, now working side by side with the quality team, gained a deeper understanding of the challenges and expectations face by their colleagues. This awareness led to more robust testing procedures and significantly reduced software bugs, resulting in a higher quality end-product.
This of course had a flow on effect for the customer support team who had integrated themselves into the cross-functional teams as well where they shared customer feedback and insights directly with the development and quality teams. This streamlined communication allowed for faster identification and resolution of customer issues. There was now a ripple effect throughout the rest of the business with employees proactively seeking input and feedback from their colleagues, meaning that the silos disappeared.
The sense of achievement from being a part of this significant change is still with me today and this is why I am still a ‘quality champion’ sharing my passion with others – because I know it CAN be done.
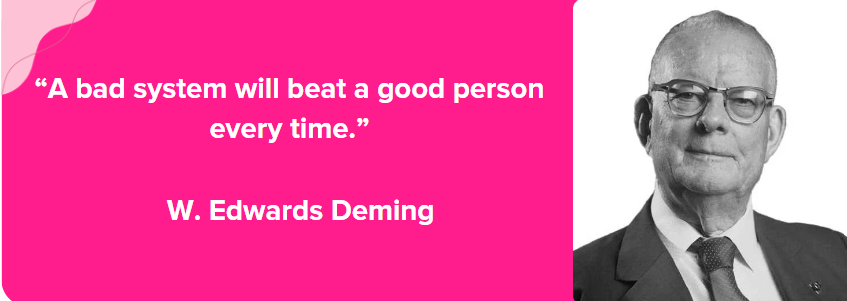
————-
A process-oriented culture is like a well-oiled machine. Just as a well-oiled machine operates smoothly and efficiently, a process-oriented culture emphasizes the importance of optimizing the entire process to achieve better outcomes. Each part of the machine plays a critical role in its overall function, and the same is true for each department or team in a process-oriented culture. By ensuring that all parts of the process are working together seamlessly, a process-oriented culture can achieve better results, just as a well-oiled machine can operate at peak performance.
Organizational Culture and Performance
A meta-analysis of 92 studies on organizational culture and performance found that a process-oriented culture was associated with better performance outcomes, including financial performance, innovation, and customer satisfaction, compared to a silo-oriented culture (Naranjo-Valencia, Jiménez-Jiménez, & Sanz-Valle, 2011).
Other research has found that the process approach is associated with improved quality, efficiency, and innovation. For example, a study of hospitals in Spain found that those with a process-oriented culture had higher levels of clinical effectiveness and patient satisfaction compared to hospitals with a silo-oriented culture (Salvador-Carulla et al., 2015). Similarly, a study of manufacturing firms in China found that those with a process-oriented culture were more innovative and had higher levels of quality and productivity than firms with a silo-oriented culture (Wei, Liu, & Chen, 2018).
Overall, the research suggests that the process approach is associated with better performance outcomes, including financial performance, innovation, quality, and customer satisfaction, compared to the silo approach.
———–
What level of process-oriented approach is your business at?
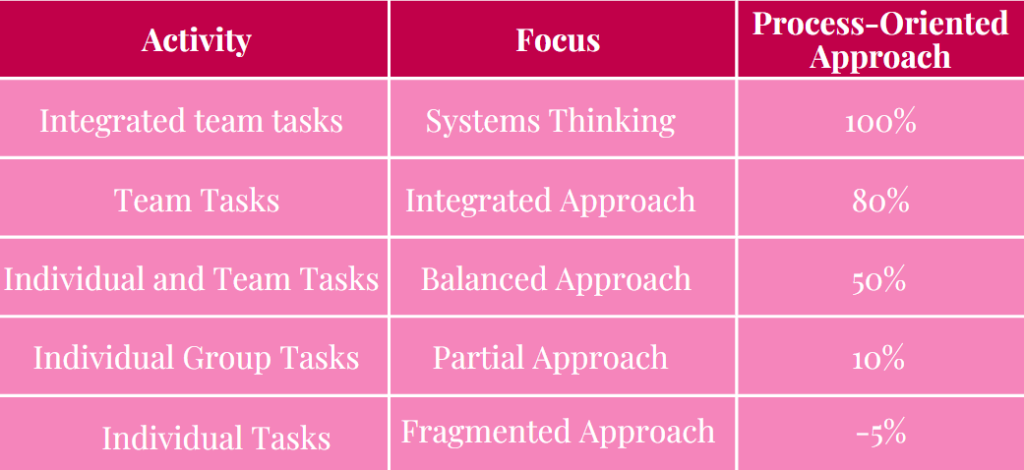
———-
- Systems thinking (or Holistic approach): This term represents a comprehensive view that considers the interrelationships, interdependencies, and dynamics within a system. It emphasizes understanding the whole system and its parts, as well as the interactions among them.
- Integrated approach: This term signifies an approach that seeks to unify and connect different elements or components within a system. It recognizes the importance of integrating various aspects or perspectives to gain a more complete understanding of the system.
- Balanced approach: This term suggests an approach that aims to strike a balance between considering the broader system and recognizing individual elements or components. It acknowledges the interconnections while allowing for focused examination of specific aspects. Most businesses at best manage the Balanced Approach.
- Partial approach: This term reflects an approach that focuses on specific aspects or components of a system while acknowledging that it represents only a part of the overall picture. It recognizes that a comprehensive understanding may require considering additional elements or factors.
- Fragmented approach: This term describes an approach characterized by a lack of integration, with a focus on isolated or disconnected parts without considering their relationships or the broader context. It often leads to an incomplete or limited understanding of the system.
——
Keep in mind that these terms represent a continuum, and the boundary between them may not always be sharply defined. The scale serves as a general guideline to illustrate different levels of consideration given to systems thinking versus fragmentation.
——
—–
Your Next Steps
1. Introduce cross-functional teams: By bringing together diverse talents from various departments, cross-functional teams foster innovative solutions and streamline workflow efficiency. This collaborative approach ensures that different perspectives are considered, leading to well-rounded and effective strategies.
2. Engage your workforce and involve them in the process: Determine the specific knowledge and skills required to achieve project goals by assessing the expertise needed at various stages. This ensures that the team is equipped with the necessary information and capabilities to meet objectives effectively.
3. Engage an Expert to support you through this process: Hiring an expert can provide specialized knowledge and guidance, helping you navigate complex challenges with confidence and clarity. An expert’s insights and experience can streamline your efforts, ensuring that best practices are implemented effectively and efficiently.
—————–
Work with an ISO Career Expert: Elevate your career as an ISO leader.
View comments
+ Leave a comment